Technology
Hollow Fiber Membrane Spinning Machine: Top Features
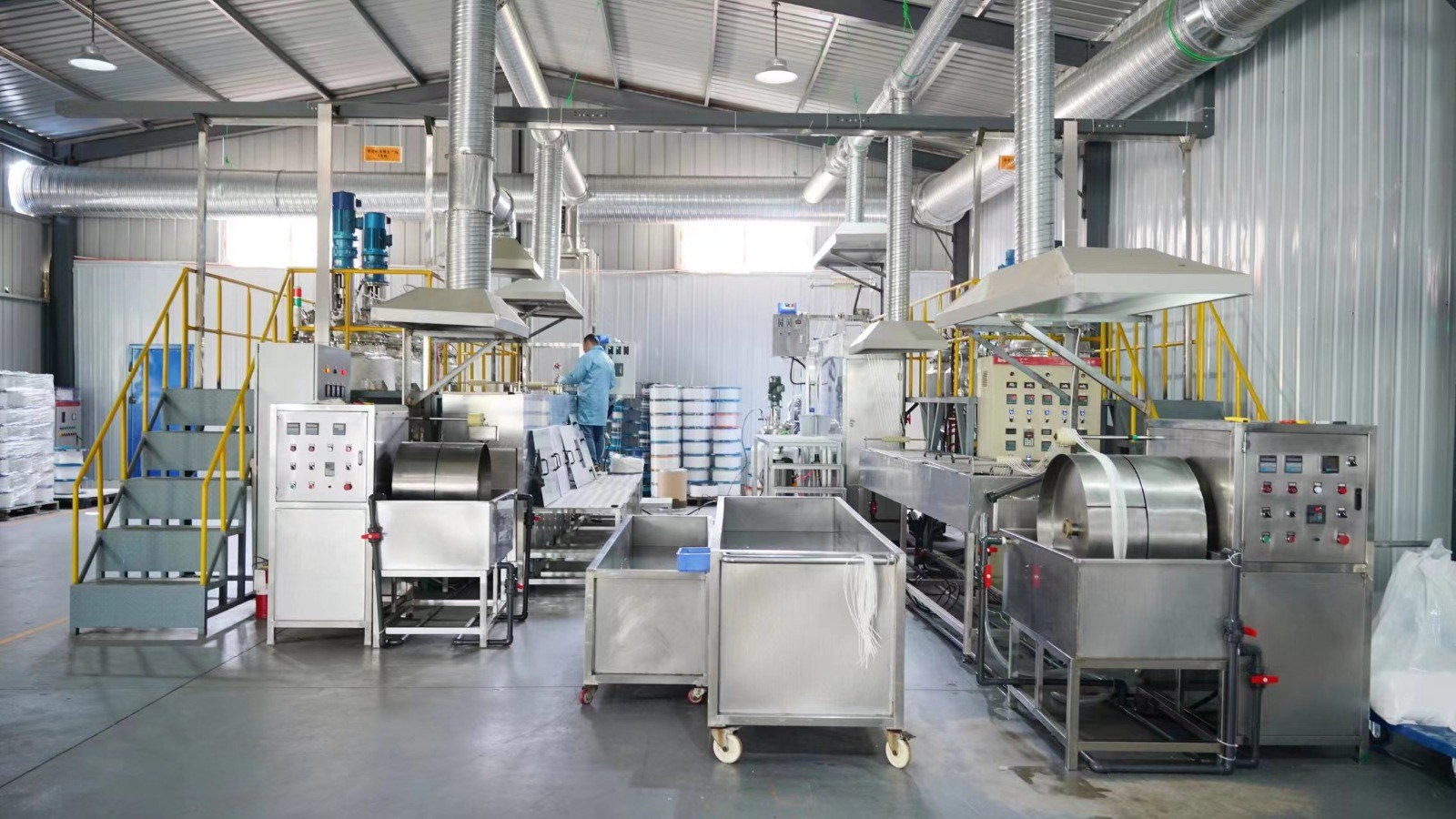
The requirement for hollow fiber membrane spinning machines is growing at a rapid pace due to their pivotal role in water purification, pharmaceuticals, biotechnology, and wastewater treatment. These machines produce filters made of hollow fibers — the “heart” of many filtration and separation processes.
If you are considering purchasing a hollow fiber membrane spinning machine, it is crucial to understand the most important features that impact performance, output quality, and long-term efficiency. This post is your practical guide for identifying the key features to consider when evaluating these machines.
Accurate Dope and Bore Fluid Control Mechanism
One of the key requirements in a hollow fiber membrane spinner is precise control of dope and bore fluid flow. These two constituents combine to form the membrane, and their flow rates must be strictly regulated to maintain consistent membrane structure and pore size.
Look for Machines That Offer:
- Peristaltic or gear digital pumps for constant flow rates
- Real-time flow monitoring systems
- Automated calibration and feedback mechanisms
Accurate fluid control results in consistent membrane dimensions and enhanced end-user performance.
Temperature and Viscosity Management
The quality of hollow fiber membranes heavily depends on the viscosity of the polymer solution (dope). Consequently, modern spinning machines are equipped with temperature-controlled tanks and pre-drawing systems to ensure uniform viscosity.
Top-Tier Machines Offer:
- Separate temperature control for dope and bore fluid tanks
- In-line heaters with thermal sensors
- Adjustable settings based on polymer type
Temperature stability is essential for repeatable results and for producing membranes with desired porosity and mechanical strength.
Adjustable Spinneret Assembly
The spinneret is the core of the hollow fiber membrane spinning machine. It is the part where the polymer solution and bore fluid merge to create hollow fibers. The design and flexibility of the spinneret assembly directly influence fiber geometry and lumen diameter.
A Good Machine Should Offer:
- Easy-to-change spinneret configurations
- A variety of spinneret sizes for different membrane diameters
- Leak-proof seal systems to prevent cross-contamination
Modular spinneret assemblies allow for quick changes between membrane types, saving time and adding operational flexibility.
High-Precision Take-Up System
After formation, the fibers are drawn through a coagulation bath and spooled with a take-up system. The take-up unit must be synchronized with the extrusion speed to avoid stretching or compressing the fibers.
Top-Quality Features Include:
- Programmable motor-controlled winding speed
- Tension monitoring sensors
- Multi-spool winding for continuous operation
Proper take-up control ensures fibers maintain their intended length, strength, and geometry during post-processing.
Advanced Coagulation and Washing Modules
Once the fibers exit the spinneret, they enter a coagulation bath, where phase inversion converts the liquid polymer into a solid membrane. After coagulation, the fibers must be thoroughly washed to remove residual solvents.
A Reliable Machine Should Have:
- Multi-stage coagulation and rinsing sections
- Adjustable bath lengths and temperatures
- Continuous circulation and filtration of bath fluids
Effective coagulation and washing are critical for impurity removal and uniform membrane performance.
Automation and PLC Control System
Modern high-speed spinning machines are equipped with Programmable Logic Controllers (PLCs) and intuitive Human Machine Interfaces (HMIs) to boost productivity and reduce human error.
Essential Features to Look For:
- Touchscreen interface with real-time process monitoring
- Customizable spinning programs and memory presets
- Alarm and fault detection systems
An automated system allows operators to manage the entire process — from startup to shutdown — with improved precision and consistency.
Material Compatibility and Cleanroom Design
Depending on the application (e.g., medical-grade membranes), the machine must be built with materials that resist harsh chemicals and meet cleanroom requirements.
Top Considerations Include:
- Corrosion-resistant stainless steel or PTFE-contact surfaces
- Sealed access panels or HEPA filters for cleanroom compliance
- Easy-to-clean components and detachable parts
For pharmaceutical and biotech applications, cleanroom-compatible membrane production is essential.
Customizability and Scalability
Whether you’re developing innovative membrane designs or running full-scale commercial operations, your machine must meet your specific production needs.
Choose a Machine That Offers:
- Scalable solutions (from lab-scale to industrial-scale production)
- Compatibility with multiple polymer solutions (PVDF, PES, PAN, etc.)
- Customizable line configurations and optional modules
Scalable machines grow with your business, and customizable features support research and development.
Safety Features
Spinning machines operate with high-pressure systems, hot fluids, and potentially hazardous solvents. Therefore, robust safety features are non-negotiable.
Ensure the Machine Has:
- Emergency stop buttons and interlocking systems
- Protective guards for hot or moving parts
- Solvent recovery and proper ventilation systems
These features safeguard your operators and reduce the risk of accidents or environmental hazards.
After-Sales Support and Spare Parts Supply
No matter how advanced your machine is, ongoing support and spare parts availability are crucial for minimizing downtime.
Choose a Manufacturer That Offers:
- On-site installation and training
- Preventive maintenance plans
- Fast access to common spare parts and consumables
Strong after-sales support ensures maximum uptime and a high return on your investment.
Conclusion
Choosing the right hollow fiber membrane spinning machine isn’t just about the price tag. It’s about aligning the machine’s technical features, automation capabilities, safety standards, and scalability with your production goals.
By focusing on the key features outlined above — including precision fluid control, temperature regulation, advanced spinneret systems, and automation—you’ll be better prepared to select a machine that offers reliability, consistency, and top-tier membrane quality.
Whether you’re a startup lab or a large-scale manufacturing facility, investing in a well-designed hollow fiber membrane spinning machine lays the groundwork for efficient, scalable, and innovative membrane production.
Technology
yt5s 5 Easy Tricks for Fast YouTube Downloads in 2025
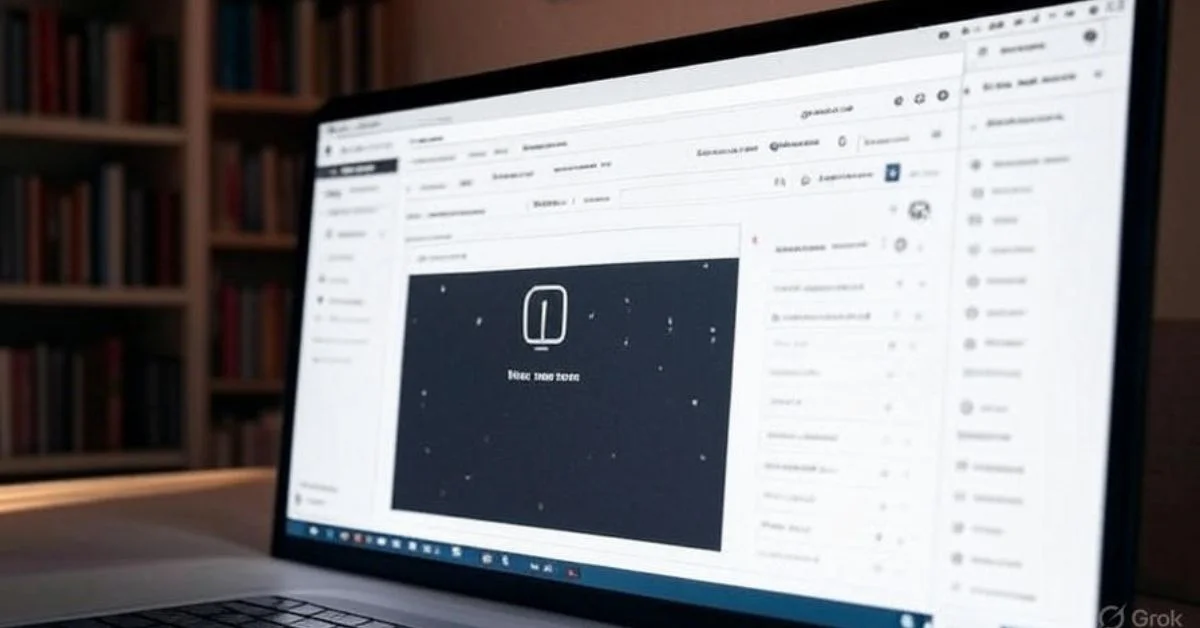
Hey, Why yt5s?
Imagine you’re stuck on a train with no signal, dying to watch that new yoga video you found on YouTube. Or maybe you’re a teacher needing a clip for class without relying on spotty Wi-Fi. That’s where yt5s swoops in. It’s a free, no-hassle tool to download YouTube videos or audio straight to your phone or laptop. Let’s walk through how it works, keep it safe, and figure out if it’s your best bet.
What You’ll Learn:
-
yt5s is a free, no-sign-up tool to snag YouTube videos or audio.
-
Stay safe by dodging shady ads and fake sites.
-
Know the legal stuff to keep things above board.
-
See how yt5s stacks up against other downloaders.
-
Fix pesky issues with quick tricks.
What’s yt5s All About?
Ever wished you could save a YouTube video for later, like a recipe clip for your next cooking spree? yt5s is an online tool that lets you download YouTube videos or audio without downloading any apps. Just pop in a video link, pick MP4 for video or MP3 for audio, and save it. It’s like grabbing a snack from the fridge—quick and easy.
-
Why it’s cool: Perfect for offline vibes, like watching tutorials at the gym.
-
Who loves it: Students, creators, or anyone needing YouTube on the go.
-
Fun fact: YouTube has over 2 billion users a month, so tools like yt5s are a hit (YouTube, 2025).
Link Idea: Check out our guide to offline YouTube hacks.
How to Download with yt5s
Using yt5s is simpler than texting a friend. Say you’re a musician who found a killer cover song on YouTube and want it as an MP3. Here’s the deal:
-
Grab the link: Head to YouTube and copy the video’s URL.
-
Go to yt5s: Open the real yt5s site (double-check the URL!).
-
Paste it: Drop the link into the box on the site.
-
Choose your vibe: Pick MP4 for video or MP3 for audio, plus your quality (like 720p).
-
Hit download: Save the file and you’re set.
Quick Tip: Make sure the YouTube link is legit. If it’s not working, try a different video or refresh the page.
Visual Idea: A screenshot showing where to paste the link on yt5s.
What Makes yt5s Awesome?
So, what’s the big deal with yt5s? Picture yourself wanting to save a crisp 4K travel vlog for inspiration. Here’s why yt5s rocks:
-
Top-notch quality: Download videos in up to 4K or audio in clear MP3.
-
Works anywhere: Phone, tablet, laptop—any browser does the trick.
-
No account needed: Jump in and start downloading.
-
Global friendly: Supports tons of languages for users worldwide.
-
Free and fast: No cost, and downloads zip by.
Cool Stat: 65% of YouTube fans want offline access, which is why yt5s is so popular (Pew Research Center, 2020).
Link Idea: Explore our list of top YouTube-to-MP3 tools.
Is yt5s Safe to Use?
Let’s talk safety. Nobody wants a virus just to save a cat video, right? yt5s is generally safe—no malware reports—but those pop-up ads can be sneaky. I once clicked a weird ad and ended up on a spammy site. Closed the tab, found the real yt5s, and was fine.
-
Stay smart: Use an ad-blocker and stick to the official yt5s site.
-
Watch out: Skip any “mirror” sites or pop-ups that look fishy.
-
Pro Tip: Keep antivirus software running for extra protection.
Stat: 24% of folks are wary of unverified online tools (PMC, 2021).
Visual Idea: A checklist for spotting legit websites.
Is Downloading with yt5s Legal?
Okay, here’s the tricky part: legality. YouTube’s rules are strict—you can’t just download videos without permission. Breaking copyright laws can cause headaches, but there’s a way to play it safe.
-
Fair use 101: Downloading for personal study or non-profit use, like a teacher grabbing a public domain clip, might be okay.
-
Check your country: Copyright laws differ, so do a quick search for your area’s rules.
-
Real story: A teacher I know downloaded a Creative Commons science video for class—totally legal.
Quick Tip: Stick to videos you have permission for, like your own uploads or public domain content.
Link Idea: Read up on YouTube’s terms of service.
yt5s vs. Other Downloaders
Not sure if yt5s is your match? Let’s compare it to other tools. Say you’re a video editor needing a high-quality clip. Here’s the scoop:
-
yt5s: Free, no setup, great for quick grabs, but has ads.
-
Y2Mate: Free and online, but ads can be more annoying than yt5s.
-
4K Video Downloader: Paid, grabs playlists and subtitles, awesome for pros.
-
SnapDownloader: Premium, super fast, with fancy options like 8K support.
Quick Tip: Need playlists? Go for 4K Video Downloader. For free and easy, yt5s is your friend.
Visual Idea: A side-by-side chart of yt5s, Y2Mate, and 4K Video Downloader.
Link Idea: Our 2025 roundup of YouTube downloaders.
Fixing yt5s Hiccups
Sometimes yt5s acts up—like when your download stalls or the video won’t play. Picture a student trying to save a lecture but hitting an error. Here’s how to fix it:
-
Download won’t start: Check your Wi-Fi or try a different YouTube link.
-
Format issues: Pick MP4 for phones or MP3 for audio to avoid glitches.
-
Slow downloads: Try late at night or switch browsers (Chrome often works best).
-
Browser woes: Clear your cache or swap to another browser.
Quick Tip: If yt5s is down, check X for user chatter about outages.
Link Idea: Common fixes for YouTube downloader problems.
Pro Tricks for yt5s Fans
Ready to get fancy with yt5s? These tips can make your downloads next-level. Imagine you’re a podcaster saving a whole playlist of interviews for offline editing.
-
Grab playlists: Paste the playlist URL to download multiple videos. Test with a short one first.
-
Snag subtitles: If the video has captions, check if yt5s can save them.
-
Cloud it up: Save downloads to Google Drive for easy access anywhere.
-
Real story: A friend downloaded a playlist of guitar tutorials to practice offline.
Quick Tip: Preview playlists to make sure all videos are downloadable.
Visual Idea: A step-by-step graphic for playlist downloads.
Solving Common Headaches
Using yt5s can hit some bumps. Here’s how to smooth them out, based on what users say online:
-
Safety fears: Stick to the official site and use antivirus to dodge scams.
-
Legal worries: Only download what you’re allowed to, like your own videos.
-
Download fails: Try another browser or wait a bit for server issues to clear.
-
Annoying ads: An ad-blocker can save your sanity.
-
Free vs. paid: yt5s is free, but for pro features, try SnapDownloader.
Cool Stat: Video downloads jumped 200% during the pandemic, showing how much we lean on tools like yt5s (PMC, 2022).
FAQs
-
What’s yt5s for?
It’s a tool to save YouTube videos or audio as MP4 or MP3 for offline use, like studying or editing. -
Is yt5s safe?
Pretty safe if you use the real site and an ad-blocker to skip risky ads. -
Is yt5s legal?
Downloading without permission might break YouTube’s rules; stick to fair use. -
Can yt5s grab playlists?
Yup, just paste the playlist link and pick your format to save multiple videos. -
Why’s yt5s not working?
Check your connection, link, or cache; try another browser if it’s still acting up. -
How’s yt5s vs. Y2Mate?
yt5s has fewer ads and similar features, but Y2Mate can be less reliable.
Technology
Y2Mate Review 2025: Safe, Legal, or Risky Alternatives
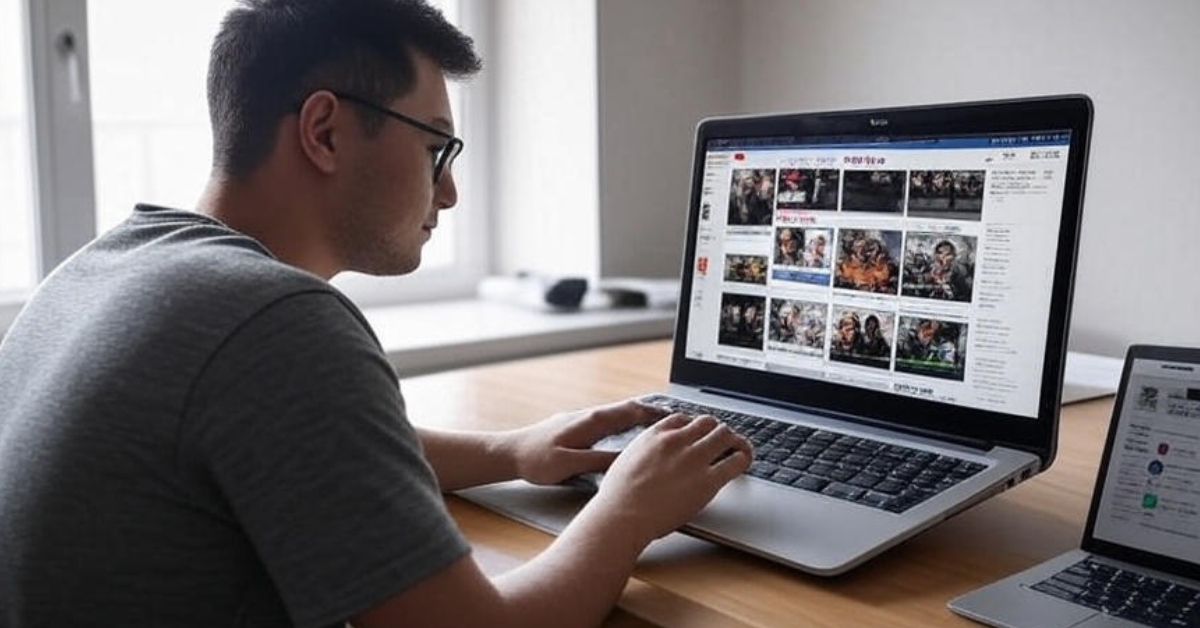
Have you ever come across a YouTube video you wanted to save for offline viewing? That’s where tools like Y2Mate step in. In 2025, it remains one of the most popular free options for downloading YouTube videos or audio. But with growing concerns about safety, legality, and potential risks, it’s important to understand how it really works. In this review, we’ll break down the pros, cons, and safe alternatives—so you can decide wisely without the hassle.
Key Takeaways
- Y2Mate lets you download YouTube stuff for free, but ads and pop-ups can lead to trouble like malware, based on user stories from 2025.
- It’s not always safe—many folks report redirects to sketchy sites, but with an ad blocker, you might dodge the worst.
- Legally, it’s tricky: downloading copyrighted videos for personal use is fine, but it can break rules and harm creators.
- Better options, such as 4K Video Downloader, offer ad-free peace of mind without the risks.
- Traffic is huge, over 100 million visits a month, but trust is low with a 2/5 rating on sites like Trustpilot.
What Is Y2Mate?
Y2Mate steps in as a simple online spot to convert and download YouTube videos to MP3 or MP4. It started years ago and now handles stuff from other sites like Facebook too. No need to sign up or install anything—just paste a link and go.
Core Features
- Grab videos in high quality, up to 8K if available.
- Convert to audio for podcasts or music on the fly.
- Works on phones or computers, no extra apps required.
It’s handy for quick saves, but keep in mind, not everything’s perfect—we’ll get to that.
How It Works
First, copy the YouTube link. Head to y2mate.com, paste it in the box, pick your format like MP3 for sound only, and hit download. It usually takes seconds, but longer videos might drag. One trick: Add “pp” after “youtube” in the URL for a shortcut, but double-check you’re on the real site to skip fakes.
Is Y2Mate Safe?
Okay, let’s be real—safety is the big question in 2025. From what users say, Y2Mate itself isn’t a virus, but those ads? They’re like walking through a minefield. Pop-ups can redirect you to weird places, and some folks end up with unwanted software. It’s not malicious on purpose, but the risks add up.
Common Risks
- Ads that trick you into clicking and downloading junk.
- Potential for browser changes, like new homepages you didn’t want.
- Sharing your info without asking, which feels creepy.
Over 450,000 new malware bits pop up daily, and sites like this can accidentally link to them.
Real-User Examples
I read stories on Reddit where someone clicked a fake download and their phone slowed down big time. On Trustpilot, one user in 2025 said they got flashed with scam sites after a redirect—yikes! But others swear by it with an ad blocker, calling it fast and reliable for minimal ads.
Practical Tips
Want to try it anyway? Grab uBlock Origin to block those pesky ads. Scan any file you download with something free like Malwarebytes. And stick to desktop if possible—mobile seems riskier with more redirects.
Is Y2Mate Legal?
Now, onto the rules. Y2Mate isn’t illegal to use, but what you download might be. YouTube’s terms say no downloading without permission, especially if it’s someone else’s work. It’s like borrowing a book versus copying the whole thing.
Legal Concerns
- Breaks YouTube’s rules, which could get your account flagged.
- Copyright stuff: In places like the US, fines are possible for protected videos.
- Clones add confusion—some shut down over legal heat.
In 2025, with stricter online laws, it’s wiser to think twice.
Ethical Considerations
Think about the creators—they lose views and money when you download instead of streaming. Imagine you’re a YouTuber putting hours into a video, only for folks to grab it free. One story: A teacher downloads lectures for class, which feels okay, but music videos? Not so much.
Tips for Compliance
Only save public stuff or your own uploads. Try YouTube Premium for official offline mode—it’s ad-free and supports creators. Or check if the video allows downloads natively.
How to Use Y2Mate Safely
If you’re set on using it, let’s make it as smooth as possible. Tests show it can grab a 1080p video in under a minute, but prep right to avoid issues.
Step-by-Step Guide
- Copy the video URL from YouTube.
- Go to the site and paste it.
- Choose MP3 for audio or MP4 for video.
- Click download and wait—close any extra tabs that pop up.
Common Challenges
Long clips over an hour might fail midway. Ads interrupt, slowing things. And if it doesn’t work, it could be your blocker or site blocks in your area.
Performance Stats
It’s popular: Over 100 million monthly visits globally, with big numbers in India and Japan. Supports batch grabs and high-res, but speed varies with your connection.
Y2Mate Alternatives
Why stick with risks when there are calmer options? Many users switched in 2025 after bad experiences. These picks focus on safety and extras.
Top Recommendations
- 4K Video Downloader: Desktop app, no ads, handles playlists easily.
- SnapDownloader: Super fast for batches, with editing tools.
- yt-dlp: Free command-line for tech folks, no viruses reported.
- Any Video Converter: Multi-site support, great for MP3 pulls.
Comparison
Y2Mate is free and online, but full of ads. Alternatives like 4K cost a bit for premium ($20/year) but skip the drama. Users on X say yt-dlp feels safer for long-term use.
Why Switch?
Ditch the pop-ups and privacy worries. Get features like subtitles or better quality without fearing a virus. One user shared how switching fixed their slow downloads overnight.
How to Remove Y2Mate Virus
Uh-oh, did something slip through? If your browser acts up with extra ads or slows, it might be a “Y2Mate virus”—really just unwanted programs.
Removal Steps
- Scan with Norton or similar—let it quarantine junk.
- Clear your browser’s cache and extensions.
- Reset settings to factory fresh.
Prevention Advice
Use a VPN for extra shield. Update your antivirus weekly. And avoid clicking anything suspicious.
Expert Insights
Pros say daily scans catch issues early, with over 450K threats out there.
One tip: If notifications bug you, block them in settings.
User Reviews and Trends
In 2025, opinions are split. Trustpilot gives it 2/5 from 51 reviews—some love the ease, others hate the ads. On X, posts warn about viruses but praise quick grabs.
Sentiment Analysis
Positives: “Minimal ads now, super useful.” Negatives: “Redirects to malware—trash.” Mobile users gripe more about risks.
Emerging Trends
AI tools are rising for smarter downloads. Clones like y2mate.nu confuse things—stick to originals. Traffic dipped a bit with adblocker popularity, but it’s still huge.
FAQs
Is Y2Mate safe in 2025? Not fully—ads can lead to malware, but an ad blocker helps. Many users report issues, so consider alternatives.
How do I remove Y2Mate virus? Scan with antivirus, clear browser data, and reset settings. Tools like Malwarebytes work well for PUPs.
Is Y2Mate legal for YouTube downloads? Gray area: Okay for personal use, but violates YouTube TOS and copyrights, possibly leading to fines.
What are safe Y2Mate alternatives? Go for 4K Video Downloader or yt-dlp—ad-free and reliable without the risks.
Does Y2Mate have clones? Yes, like y2mate.nu—some are riskier with more malware; verify the URL first.
Why is Y2Mate not working? Could be ad blockers, site blocks, or slow connections—try incognito or a VPN.
So, there you have it. Y2Mate can be a quick fix, but with all the risks in 2025, why not try a safer alternative? Give one a shot next time you need a download—you’ll thank yourself. If you’ve got stories or questions, drop them below!
Technology
Bunkr-Albums Discover 7 Powerful Reasons to Explore Now
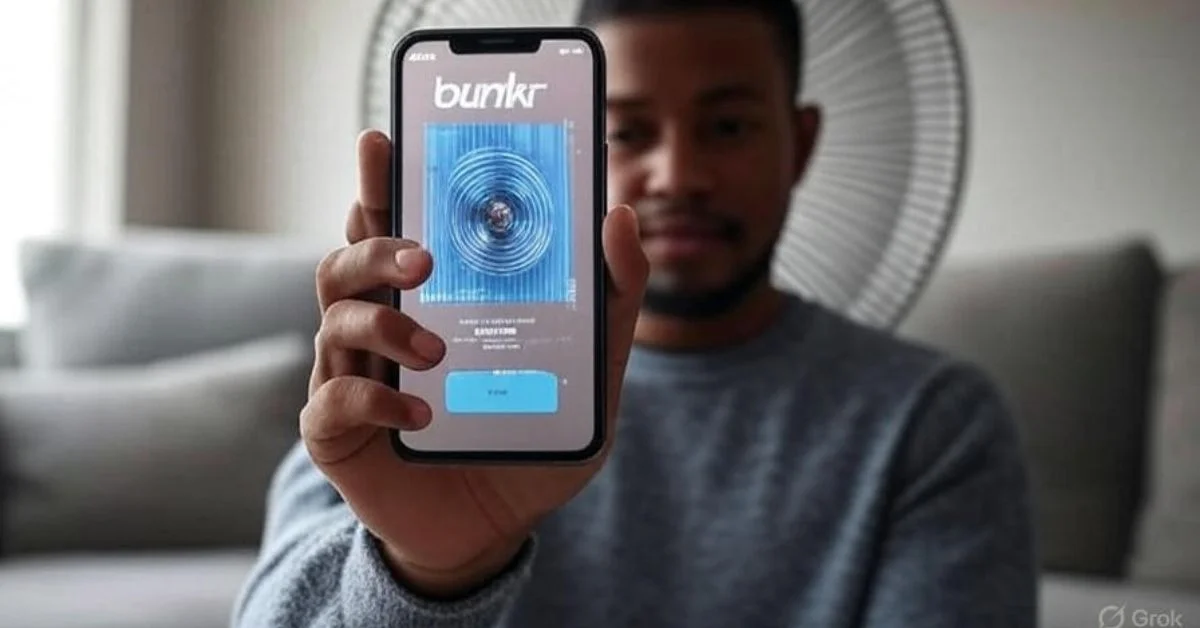
Introduction
you’re chilling with your headphones, scrolling for new tunes, and you spot something called a bunkr album. It sounds like a secret club for music fans, right? In 2025, bunkr albums are the talk of the town, blending music with cool tech like 3D sound and digital collectibles. Let’s break down what makes them so awesome and how you can get in on the fun.
Key Takeaways
-
Bunkr albums mix music with tech like 3D audio and NFTs for a one-of-a-kind vibe.
-
They’re perfect if you want to feel closer to your favorite artists.
-
You don’t need fancy gadgets to enjoy most bunkr album perks.
-
Big names like Billie Eilish and Kendrick Lamar are all in on this trend.
-
They’re a fun, new way to make music feel personal and exciting.
What’s a Bunkr Album, Anyway?
Imagine you’re not just listening to music but stepping into a whole world the artist created. That’s a bunkr album. It’s like a regular album got a tech upgrade, mixing songs with stuff like immersive sound, interactive stories, and digital goodies you can own. The name “bunkr” nods to a private, exclusive space—like a hideout for fans.
-
What Makes Them Special:
-
3D Sound: Music wraps around you, like the band’s playing in your room.
-
Interactive Vibes: Pick your own path in the album’s story to unlock hidden tracks.
-
Digital Collectibles: Snag unique items, like virtual album art or concert passes.
-
AR Magic: Point your phone at the album cover for cool videos or effects.
-
This trend kicked off around 2024 when artists like Kings of Leon started playing with digital collectibles. Now, in 2025, it’s everywhere—60% of music fans want more than just plain songs, according to music blogs.
Why Everyone’s Talking About Bunkr Albums
Ever get bored with the same old playlists? Bunkr albums are like a breath of fresh air. They’re blowing up because they make you feel like you’re part of the music, not just listening to it. Fans on X can’t stop gushing about how these albums feel “alive” and personal.
-
Why They’re a Hit:
-
Closer to Artists: You’re not just a listener; you’re part of the story.
-
Exclusive Goodies: Limited digital items make you feel like a VIP.
-
Tech That’s Fun: New tools like 3D audio are easy to use and super cool.
-
Think of it like getting a backstage pass to your favorite band’s world. That’s why bunkr albums are the talk of 2025.
Awesome Bunkr Albums to Try in 2025
Let’s get real—some artists are nailing this trend. Here are three bunkr albums that fans are obsessed with:
-
Taylor Swift’s “Echoes: The Immersive Experience”:
-
You get songs that change based on how you’re feeling, thanks to AI.
-
Cool digital trading cards with lyrics you can own.
-
Fans on music forums say it’s like “living inside Taylor’s music.”
-
-
Kendrick Lamar’s “The Interactive Chronicles”:
-
A rap album where you pick the story, unlocking new verses.
-
Includes virtual concert tickets if you grab the right digital collectible.
-
Blogs call it a “must-try” for hip-hop fans.
-
-
Billie Eilish’s “Hologram Dreams”:
-
Pop it open with AR glasses for wild 3D visuals.
-
Offers exclusive digital art you can’t get anywhere else.
-
X users say it’s “like a concert in your phone.”
-
These albums show how bunkr albums turn music into something you can explore and collect.
How Do Bunkr Albums Actually Work?
Okay, so how do you dive into one of these? It’s not as tricky as it sounds. Bunkr albums use tech to make music more than just background noise. Here’s the deal:
-
3D Audio: Pop on headphones, and it’s like the music’s all around you. No need for expensive gear—just your phone and decent earbuds.
-
Choose-Your-Own-Adventure: Some albums let you pick story paths, like a game. Choose right, and you might unlock a secret song.
-
Digital Collectibles: These are like rare trading cards but digital. You might buy one for exclusive album art or a virtual meet-and-greet.
-
AR Fun: Use your phone to scan the album cover, and boom—virtual videos or behind-the-scenes clips appear.
You don’t need to be a tech wizard. A smartphone and some curiosity get you started. For example, I tried scanning a Billie Eilish album cover with my phone, and a 3D video of her popped up—it was wild!
Why You’ll Love Bunkr Albums
So, why bother with bunkr albums? They solve problems you didn’t even know you had with regular music. Here’s what makes them stand out:
-
Feel the Music: You’re not just listening; you’re part of the artist’s world.
-
Own Cool Stuff: Digital collectibles are like rare vinyl, but for 2025.
-
Next-Level Sound: 3D audio makes every song feel like a live show.
-
Worth the Price: Basic versions start at $10, and even premium ones come with perks like concert access.
Imagine you’re a Kendrick Lamar fan. With his bunkr album, you could unlock a hidden verse by picking the right story path. It’s like being in on a secret with your favorite artist.
Tackling Bunkr Album Challenges
Let’s be honest—bunkr albums can feel a bit overwhelming at first. Fans on X mention a few hiccups, but they’re easy to handle. Here’s how to deal with common issues:
-
Tech Seems Tricky: New to digital collectibles or AR? Start with free apps like OpenSea for collectibles or your phone’s camera for AR. Most artists have how-to guides on their sites.
-
Price Worries: Basic bunkr albums cost $10-$20, but fancy digital collectibles can hit hundreds. If you’re on a budget, stick with the standard version.
-
Finding Hidden Stuff: Some content hides behind passwords or special links. Check artist socials or fan groups on Reddit for codes and tips.
These bumps are small potatoes compared to the fun you’ll have. A quick browse on X showed me fans sharing codes to unlock extras—it’s like a treasure hunt!
Bunkr Albums vs. Regular Albums
Wondering how bunkr albums compare to the usual stuff on your music app? Let’s break it down:
-
Bunkr Albums:
-
Awesome Stuff: Interactive, exclusive, packed with tech.
-
Downsides: Might take a minute to learn; premium features cost more.
-
Perfect For: Fans who want music to feel like an adventure.
-
-
Regular Albums:
-
Awesome Stuff: Simple, cheap, works everywhere.
-
Downsides: Can feel same-old, less engaging.
-
Perfect For: People who just want to hit play and go.
-
If you love getting lost in music, bunkr albums are your jam. If you’re cool with basic playlists, regular albums still do the trick.
Five Tips to Rock Bunkr Albums
Ready to jump in? Here are five easy ways to make bunkr albums even more fun:
-
Ease In: Start with a simple album like Taylor Swift’s to get the hang of it.
-
Grab Good Earbuds: Cheap ones work fine, but good ones make 3D audio pop.
-
Join the Fan Club: Hop on Reddit or X to find tips and secret codes.
-
Be Smart with Collectibles: Only buy digital items from trusted sites like OpenSea to stay safe.
-
Stay in the Loop: Follow your favorite artists for news on new features or drops.
I tried these tips with a Billie Eilish album and found a hidden track by joining a fan group. It felt like cracking a code!
What’s Next for Bunkr Albums?
Bunkr albums are just getting started. In 2025, they’re huge, but the future sounds even crazier. Here’s what music insiders are buzzing about:
-
Virtual Concerts: Albums linked to shows in virtual worlds like the metaverse.
-
AI-Tuned Songs: Tracks that shift based on your mood or listening habits.
-
Fan Power: Tech could let fans co-own albums or share in the profits.
As tech gets cheaper, more artists will join the bunkr party. Fans on X are already hyped about “music you can live in.”
FAQs
-
What’s a bunkr album?
It’s music mixed with tech like 3D sound, digital collectibles, and AR for a fun, immersive vibe. -
Do I need fancy gear?
Nope! A phone and headphones are enough; AR glasses are just a bonus. -
Are bunkr albums pricey?
Basic ones start at $10; digital collectibles cost more but come with cool perks. -
Can I resell digital collectibles?
Yup, on sites like OpenSea, often with a cut going to the artist. -
Will bunkr albums take over?
They’re a fun new option but won’t replace regular albums anytime soon. -
How do I get started?
Check artist websites or apps like OpenSea for albums and extras.